Project Description
The New American Home® is an annual showcase project co-sponsored by the National Association of Home Builders’ (NAHB) National Council of Housing Industry and Builder Magazine. The NAHB asked Stephen and Bart Jones of Merlin Contracting and Developing to build the New American Home 2004 in the Sahara Lakes community, just west of downtown Las Vegas. The home is designed to reach a Home Energy Rating System (HERS) score of 90, a score above the current ENERGY STAR minimum rating requirement of 86, and uses a number of high-performance technologies.
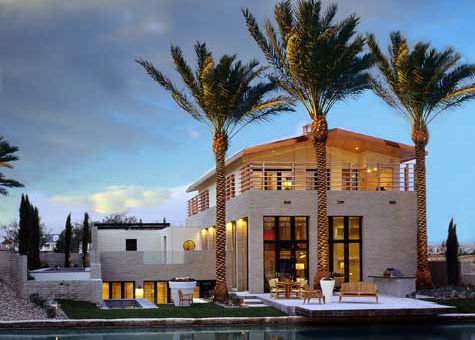
“Technologies used in this home include a foundation system and above-ground exterior walls of insulated concrete forms to provide excellent insulation for the basement; windows that limit solar heat gain; a roof system built with structural insulated panels to provide good insulation and air tightness; a heat-recovery ventilator to ensure efficient, good indoor air quality by tempering incoming hot outdoor air with cooler indoor air; and a superior efficiency condensing units with a seasonal energy efficiency ratio (SEER) between 14.7 and 16 to provide excellent cooling capacity while using minimal energy. As a result of improvements and advanced technologies, the home will use 51% less energy for heating and 54% less energy for cooling than a reference house of comparable size in this climate.[1]” The 5,000-square-foot home includes a pool that overlooks Lake Sahara. Special measures will be taken to isolate the pool from the adjacent living space. Other aesthetic features include:
- A loft design that offers versatility for interior design and layout options
- A “floating roof” in the master bedroom
- A home cinema with direct light access
- Sixteen-foot ceilings with skylights
- Mosaic flooring in the living room and master suite
- A 400 square-foot terrace with spa
The New American Home 2004® was pitched to Merlin Contracting and Developing, llc as a concrete home. But the suggestion to use insulated concrete forms (ICFs) was a new concept that required Merlin Contracting and Developing to research whether the foam forms would pass muster as a reliable building system and meet with the local building inspector’s approval. In fact, after the completion of The New American Home 2004® using ICFs, Merlin Contracting and Developing was now solidly sold on using ICFs on future projects…and even convinced their concrete subs to switch once they saw the efficiency in action. The labor-saving virtues of ICFs enabled the walls to rise quickly while also creating an open shell, which allowed maximum flexibility in room sizes and layout and a full-span, recycled steel roof frame. [1]Research that Works – Building America – U.S. Department of Energy, December 2003 DOE/GO-102003-1837 The ICFs also eliminated the plate line, an inherently problematic transition between concrete foundation walls and wood or steel framing, thus significantly reducing thermal loss. The self-insulated concrete, meanwhile, helped boost the overall efficiency of exterior walls’ thermal mass to R-50 without requiring any extra insulation. “It was 10 degrees cooler in the basement area even before we had the windows in,” says Bart Jones, noting that ICFs also resulted in a deeper, straighter wall structure than he could hope for (or even afford) with sticks in a desert climate. “The only way to combine the loft design with efficient construction is with industrialized housing techniques and systems such as ICFs and SIPs” said Lex Van Straten, architect. “We’re not trying to change the world (with this house), but to build an awareness of materials and systems that address issues of depleted resources, durability, and longer life-cycle.”